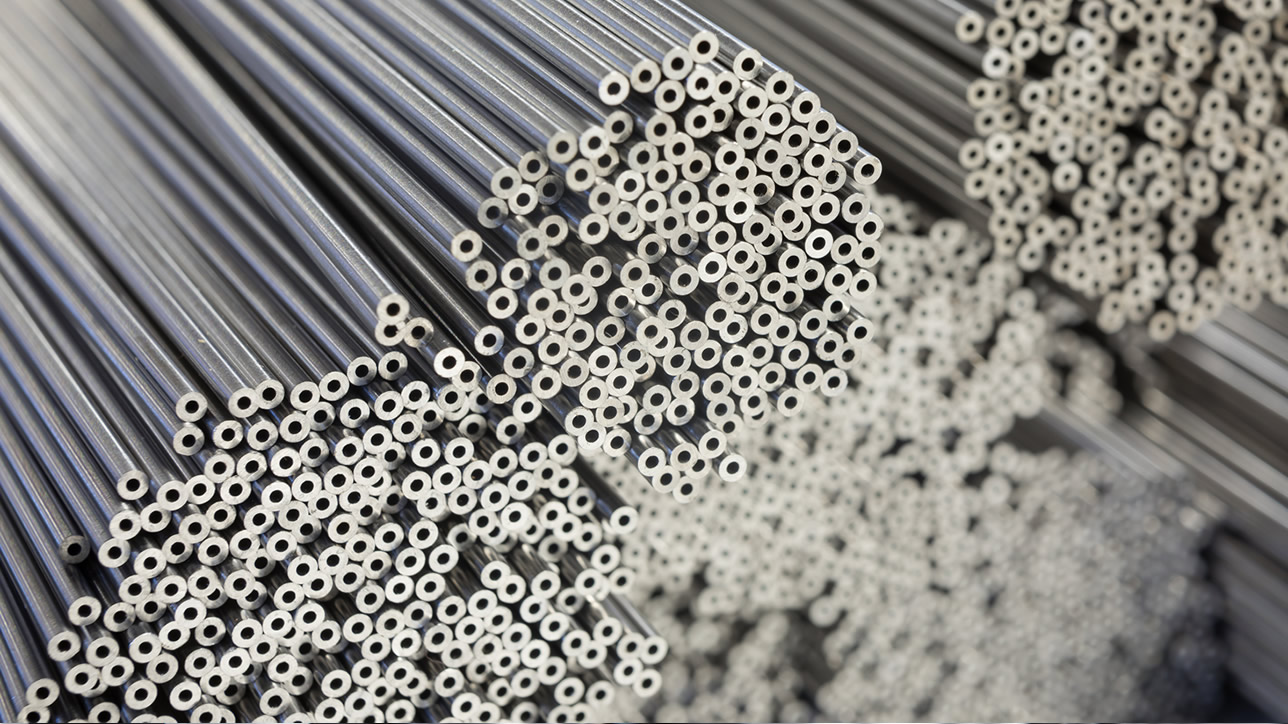
Controlled Industrial Tubing Manufacturing Methods
Accu-Tube uses multiple cold draw benches, annealing furnaces, vapor degreasers, straighteners, polishers, and lathes to produce stainless steel and high-nickel alloy tubing in more than 20 alloys that meet the highest quality standards in: welded-and-drawn (DOM) or cold-drawn (CDOD) form, in straight lengths (up to 32 feet), or in coils.
Drawn-Over-Mandrel (DOM) Tubing
DOM tubing is made from a cold-drawn welded tube that is drawn through a die and over a mandrel. This technique is often used with larger-diameter tubes with high OD-to-wall ratios. With pressure rating up to 21,000 PSI, these tubes are a reliable alternative to seamless products. Made to ASTM A249 specifications.
Benefits:
- Uniform wall thickness with more exact OD and ID tolerances
- Uniform grain structure and controlled hardness
- High yield and tensile strength
- Smooth and clean OD and ID surfaces
- Superior concentricity OD and ID
- No visible weld flash
Cold-Drawn Outside Diameter (CDOD) Tubing
CDOD tubing is made by reducing the diameter of a tube by drawing it through successively smaller dies without heating the material, which increases its tensile strength. Cold-drawn tubing is a good choice for applications where tolerances, concentricity, straightness, and surface condition are important factors. Made to ASTM specifications.
Benefits:
- More durable than welded tubing
- Most cost-effective tubing manufacturing process
- Smoother, sleeker OD finish (compared with “as weld”)
- Fractional and custom sizing
- Less ovality
Tubing


